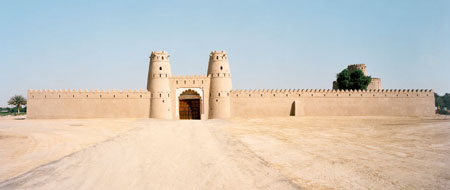
Historically, the daily life of the inhabitants of Al Ain, today the second largest city in the Emirate of Abu Dhabi, took place in the palm gardens of the oasis and the surrounding settlements and markets. To protect the oases, watchtowers and forts were erected. The Jahili Fort located in the modern-day centre of the city is the largest of Al Ain’s forts. Built in the 19th century by Sheikh Zayed the First, it can be seen from the Al Ain oasis to the west of the city. With its distinct three-tiered profile, the fort is now a national monument, pictured on the 50 Dirham note and often used as a logo or model for new architecture. The old fort was erected at the end of the 19th century.
The fort was recently restored by Roswag & Jankowski Architekten, Berlin.
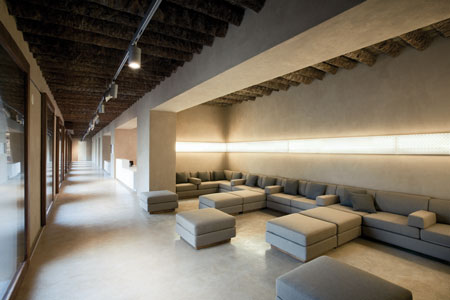
The interior surfaces remain true to the historical appearance. The ceiling consists of palm rafters and palm leaves. A local clay plaster has been used for the interior wall surfaces. In the exhibition areas a grey coloured fine clay finishing plaster made by Claytec was used to create a neutral background for the exhibition spaces. The floors likewise follow historical precedence and are made of rammed earth stabilised with a wax to cope with greater wear and tear.
All new insertions such as doors and furniture, made of corian or wood composite, are coloured white differentiating them from the surrounding building. The external render of the existing walls was examined and repaired where necessary. Previous renovation works had employed a non-traditional plaster with added gypsum for the crenelations. This plaster is too rigid and already exhibited defects; it was replaced with a clay plaster. The building was then given an overall finishing coat of clay plaster. The earth plaster is maintained at regular intervals as is traditional with this historical material. When used as an external render, clay plaster should be regarded as a weathering surface that needs ongoing maintenance, typically every two years, sometimes after sustained periods of heavy rain. Sandstorms are also a cause of erosion.
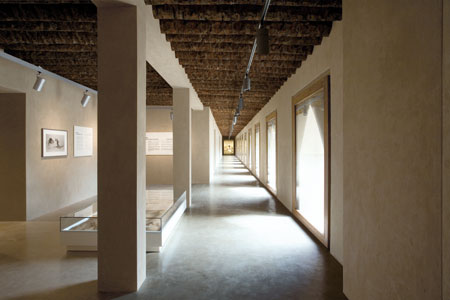
Most of the spaces will house a permanent exhibition “Mubarak bin London: Wilfried Thesiger and the Freedom of the Desert” showing photographs taken in the 1940s by the researcher and explorer Wilfried Thesiger who in the 1940s crossed the deserts of the Arabian peninsula repeatedly travelling with Bedouins and documenting what he saw with a Leica camera.
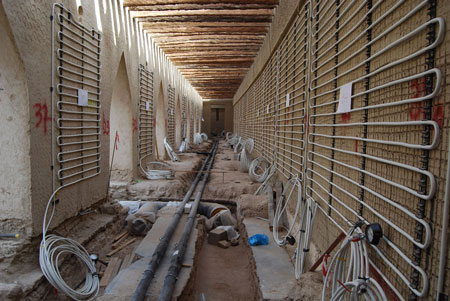
The 90 cm thick external earth walls offer excellent thermal insulation. The additional insulation on the roof improves still further the indoor room temperature and together with the solar protection windows on the façade provide effective protection against the extreme heat outdoors. The building is kept at a constant 24°C using a water-based cooling system integrated into the plaster layer of the walls. This minimizes the need for additional air cooling so that only fresh air is required. The cool indoor temperature of the walls and the reduced need for cold air makes the indoor climate more comfortable and reduces the energy consumption. An actual room temperature of 24°C equates to a felt room temperature of 22°C. The plant and technical installations for the entire fort are located below ground in the buffer zone.
The construction is made of traditionally available building materials including earth, palm products and to a lesser degree also timber. The quartered palm trunks can span a room of about 2.70 m and dictate the strongly partitioned structure of the historic buildings. The walls consist of air-dried earth blocks which can be built directly on the sandy ground without the need for foundations. A matting made of palm fronds covered with earth is laid on rafters made of split and quartered palm trunks arranged at an incline. The small amount of timber available was used for the door and window frames.