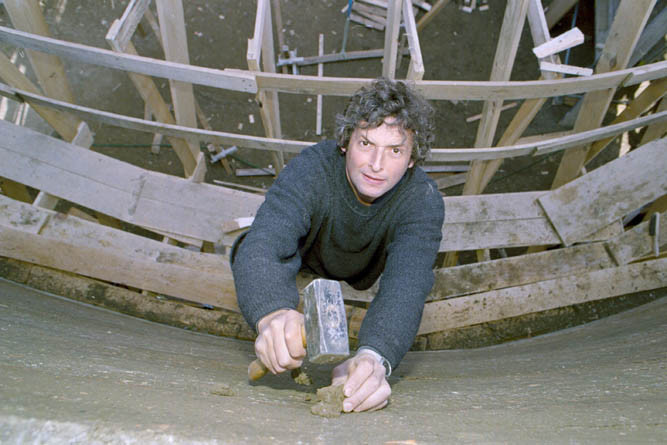
Martin Rauch, founder and managing director of Lehm Ton Erde (LTE) in Schlins, Austria, is internationally known as a leading expert in the field of rammed earth mining. He founded the company in 1984 as the sole manufacturer of ceramics and clay construction, and then founded Lehm Ton Erde Baukunst in 1999. The current studio and operations centre were built in 1990, where he presented his accumulated knowledge of clay construction at the time. Over the course of more than 35 years of working with clay, Rauch and LTE have completed over 100 projects around the world, published 3 books and led the industry in rammed earth innovations.
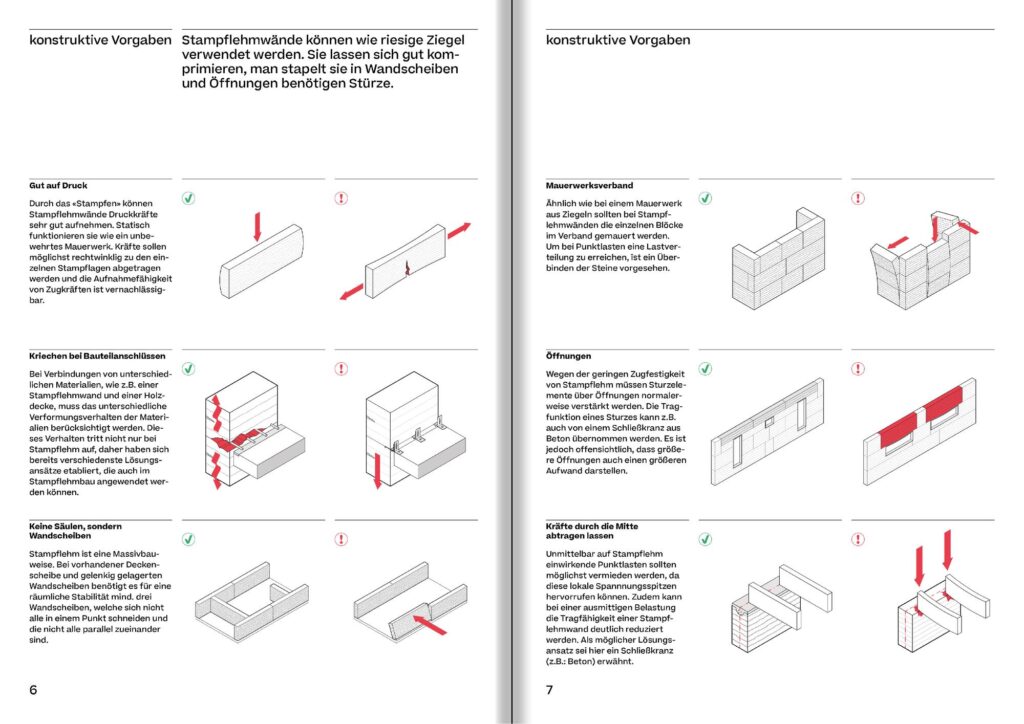
After the development of a unique precast plant, Lehm Ton Erde is now entering a new phase in which it is a matter of establishing rammed earth as a sustainable building material in order to counter the ecological burdens of the construction industry. ERDEN means clay. It is a grounding of building in natural materials and processes. Clay earth continues to be the roof for everything that has to do with rammed earth. ERDEN is a leader in clay construction prefabrication and is revolutionizing the construction industry. With the ERDEN factory hall, a new plant and headquarters for the production of precast clay elements. The team is made up of people from diverse backgrounds, including design, craft, teaching, research, and management expertise.
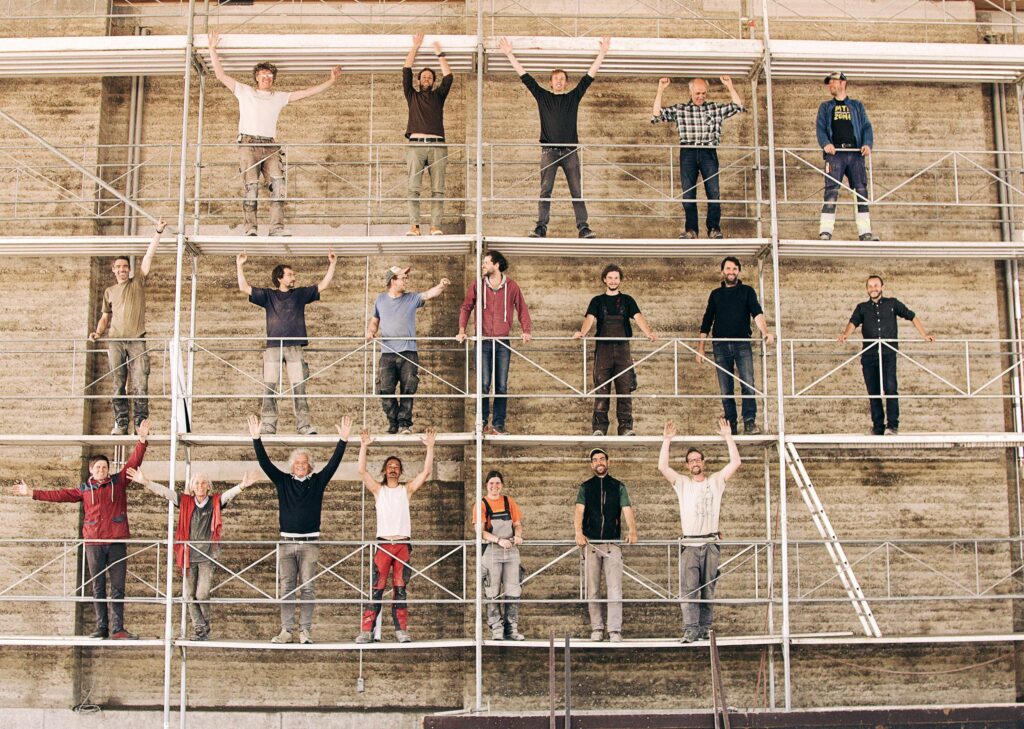
The ecological résumé of rammed earth is second to none. No other material has a smaller footprint on our planet. The raw material and the finished product are one and the same. Soil from the ground is dug up and processed. We add a little gravel or clay to optimize them, mix them with water and voilà!

This diagram emphasizes the cyclical nature of rammed earth construction, which starts and ends with the natural earth, with minimal environmental impact. This aligns with Martin Rauch’s philosophy of sustainable building, where the material’s life cycle, from construction to deconstruction, supports ecological balance.
1- Earth Site: Earth is extracted directly from the building site or a nearby location, using local resources to minimize environmental impact. This is where the raw material for the rammed earth process begins.
2- 100% Earth: The material used for construction is pure earth, without additives. The earth is gathered and sometimes modified by adding gravel or sand, depending on its natural composition.
3-Filling the Formwork: The extracted earth is placed into formwork, which is essentially a mold that shapes the walls. The formwork holds the earth in layers before it is compacted.
4-Compacting Earth: Once the earth is inside the formwork, it is compacted. This can be done manually or with the help of mechanical tools such as pneumatic hammers. The compaction process is crucial for the stability and durability of the walls.
5-Construction: The walls are constructed by repeating the process of filling and compacting. The compacted earth forms solid, load-bearing walls without the need for additional finishing materials like stucco or plaster.
6-Seamless Finishing: After the compaction and construction of the walls, seamless finishing techniques are applied. This helps to smooth out the surface and enhances the natural aesthetics of the rammed earth, maintaining the integrity and beauty of the material.
7-Transport: If needed, components of the rammed earth can be prefabricated and transported to the site. Prefabricated elements simplify the construction process, especially for large or complex structures.
8-Building in Use: The rammed earth structure is then ready for use. These buildings have high thermal mass, providing excellent insulation properties, which make them energy efficient and comfortable to live in, regulating temperature naturally.
9-Deconstruction: At the end of the building’s life cycle, it can be deconstructed. The natural earth material can be reused or returned to the site, making it a completely recyclable and sustainable material.
10-Earth Back to Site: Once the building is deconstructed, the earth is returned to the site, completing the cycle. This step emphasizes the eco-friendly nature of the process, where no waste is generated, and the material is fully reused.
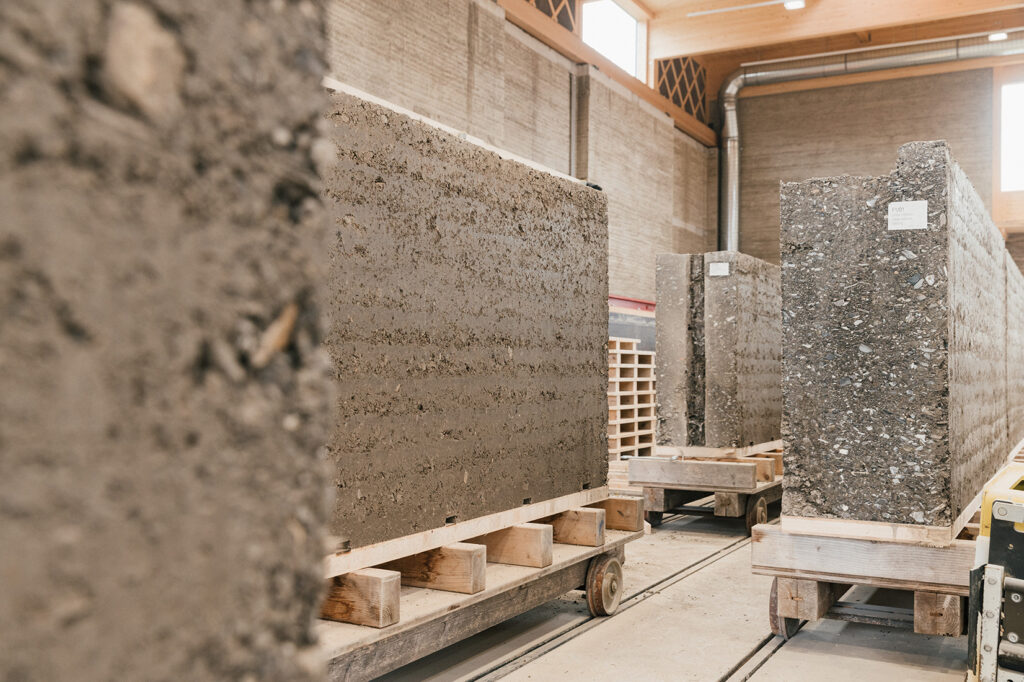
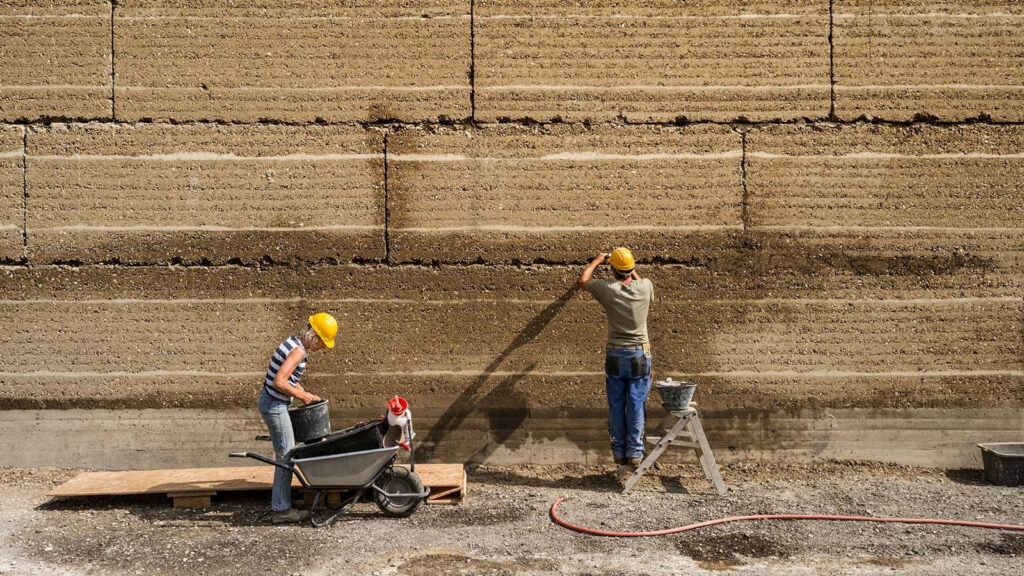
Despite its ecological, functional and aesthetic qualities, rammed earth has hardly been used in recent times. Especially because the experience with the material has been lost. For us, every rammed earth building was, if you will, a prototype. The costs were correspondingly high. Thanks to Martin Rauch’s 35 years of work, rammed earth is now losing this exclusivity. With the introduction of the ERDEN prefabrication process, we have simplified clay construction and made it more affordable. This means that the desire to build their own mud house is becoming a reality for more and more people. But there is still a long way to go. Regulatory hurdles and a broader knowledge of working with rammed earth still pose challenges. But the upswing has begun. The environment urgently needs natural building solutions. Why doesn’t everyone build with clay? Well, it’s only a matter of time.
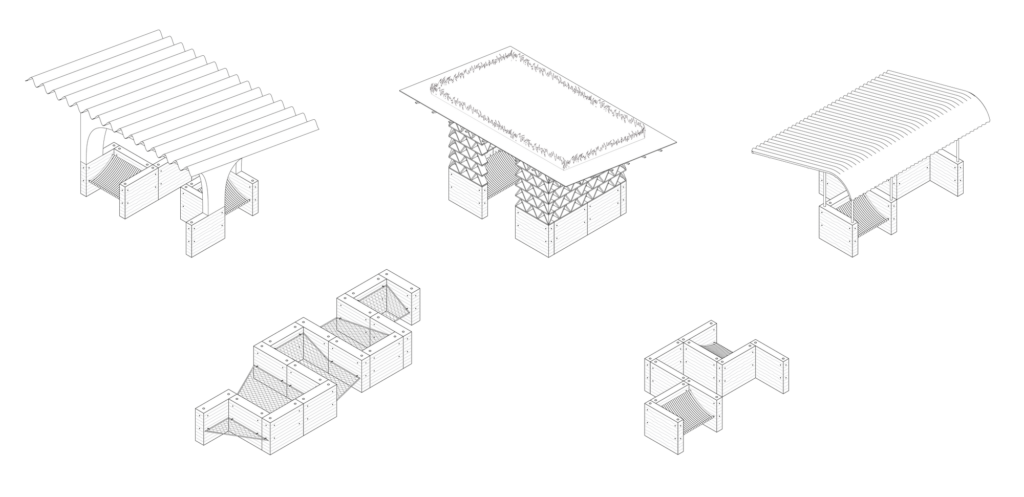
An urban-rural furniture
There’s nothing new about Earth’s resources becoming scarce, just as public space, especially in urban areas, is becoming increasingly scarce. Only what is the solution? The construction industry is one of the major polluters of our time. The Erdenbürgerin project is something of a prototype for a counter-reaction. A seating place made of 100% earth, the most sustainable building material in the World. The earth used to build this urban-rural furniture comes from our local surroundings.
Of course, this is not the silver bullet either. Rather, it is an impetus and an opportunity to ask questions. Where am I sitting here? And on what? The Erdenbürgerin asks you to take a seat and to widen your gaze. Or just to sit and commune, to chat, to relax. In a freespace, public place, as a healthy society needs. And a healthy environment. This project was developed as a cooperation between the Walgau region and earth specialists, Lehm Ton Erde.
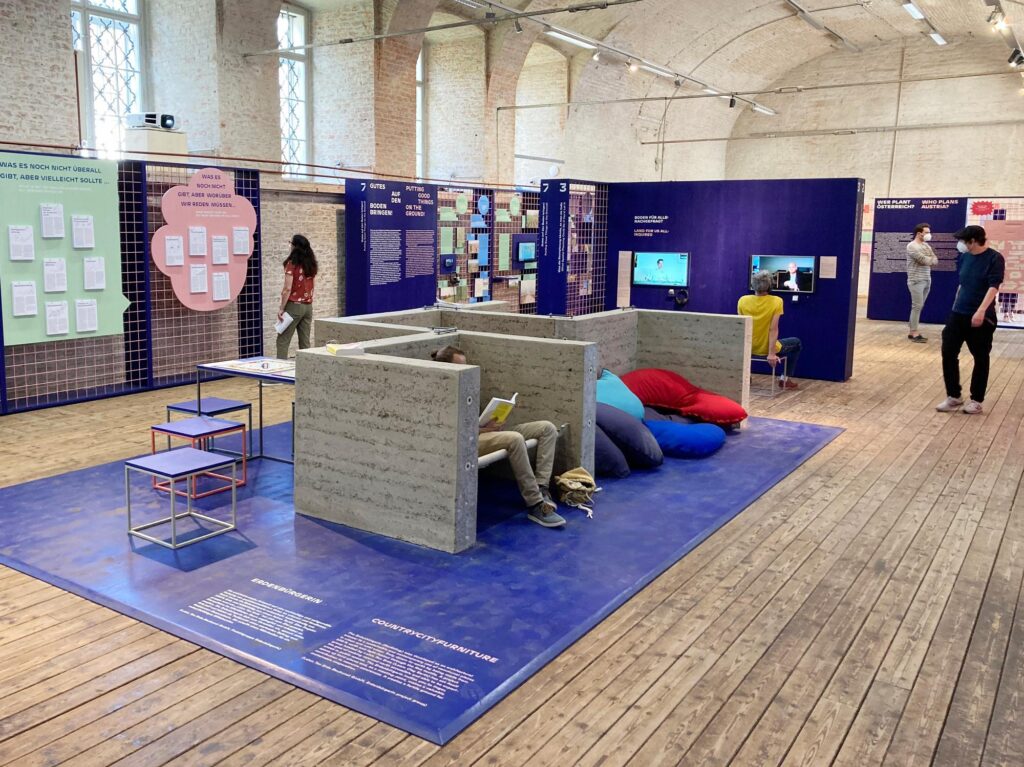
Schlins, the Mecca of rammed earth architecture, one could say, is the home of the founder of ERDEN, Martin Rauch. Since he opened his office in Schlins, several works have been created in the small town in the Vorarlberg province that have become important international precedents of contemporary rammed earth architecture. These include the Rauch Workshop, Haus Rauch, our ERDEN workshop and the Erdenhaus, which is still under construction.
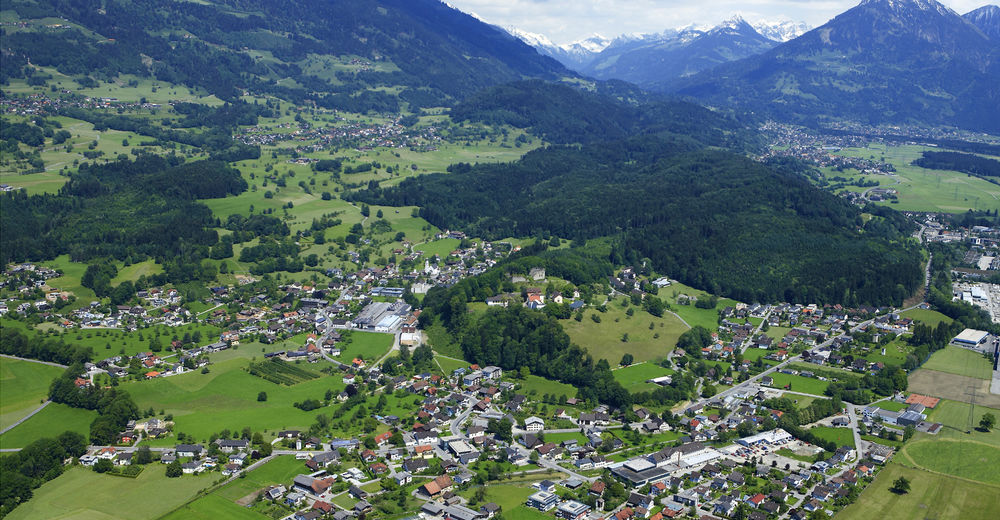
Rauch family home
Schlins: Austria
The materiality and form of the residential house are direct reactions to the steep south-sloping scarp situation of the slender plot in its landscape context – as if a monolithic block, similar to a piece of abstract and artificial nature, had been pressed out of the earth. Two clefts articulate the building of rammed earth, wedging it backwards with the scarp and establishing a frontal prelude or welcoming gesture towards the valley. The inside of the house is developed in the form of sequences of individualizable spaces that respond storey-wise to the variable conditions. As opposed to more organic, archaic clay architecture, the morphology of the building aims towards a certain clarity and sharp-edgedness. The strips of clay bricks that are inserted between the typical clay layers optically stabilise the building structure by emphasising the horizontality and heightening the light and shadow effects.
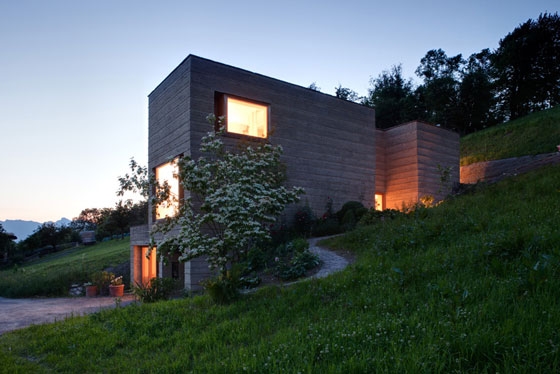
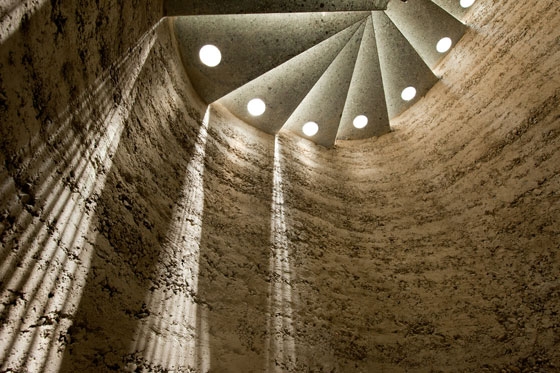
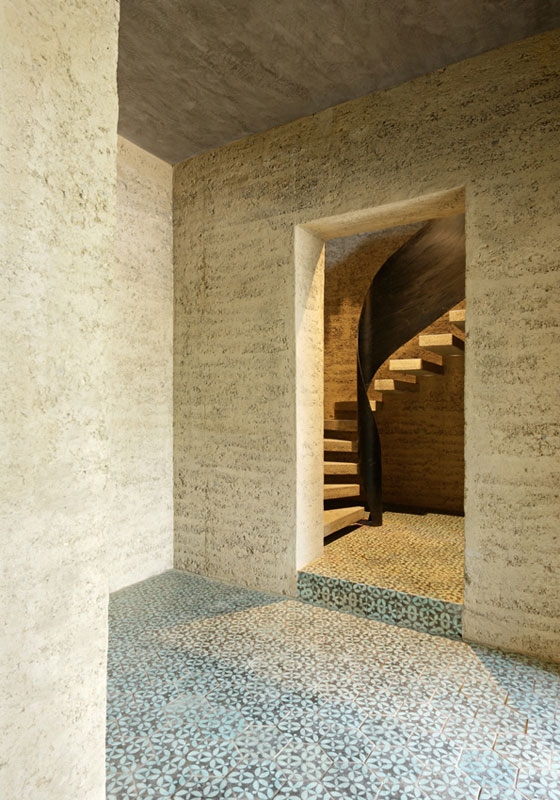
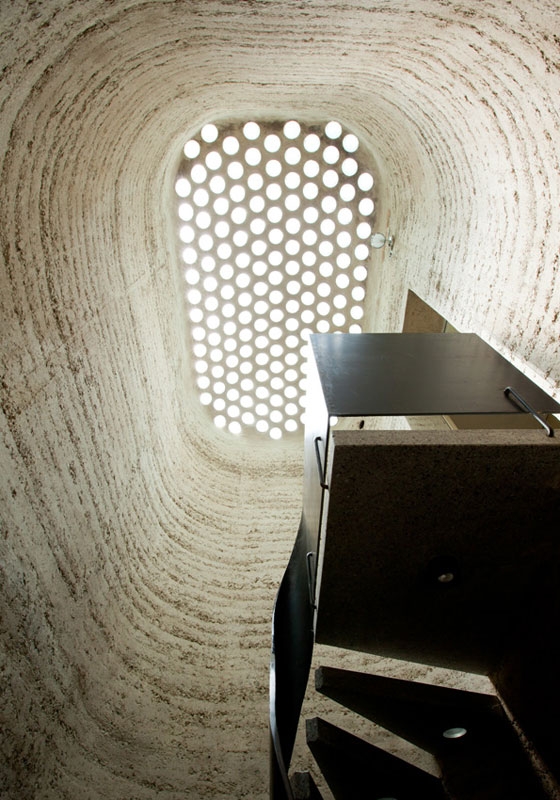
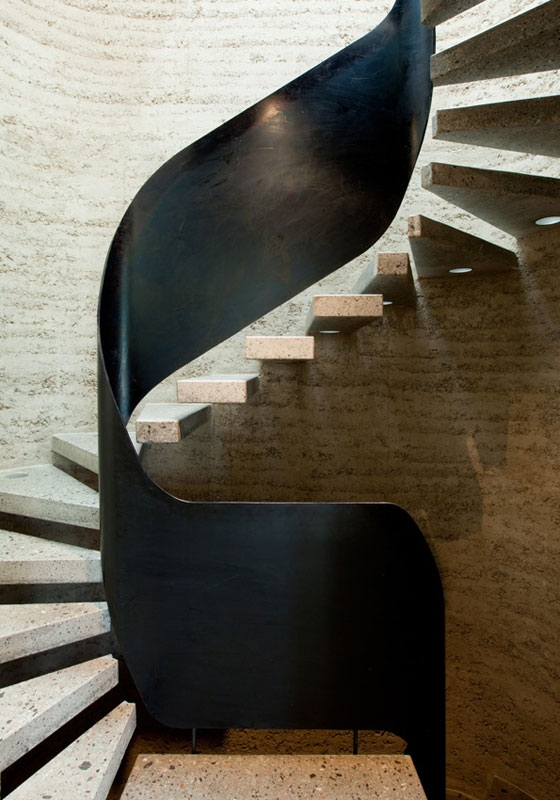
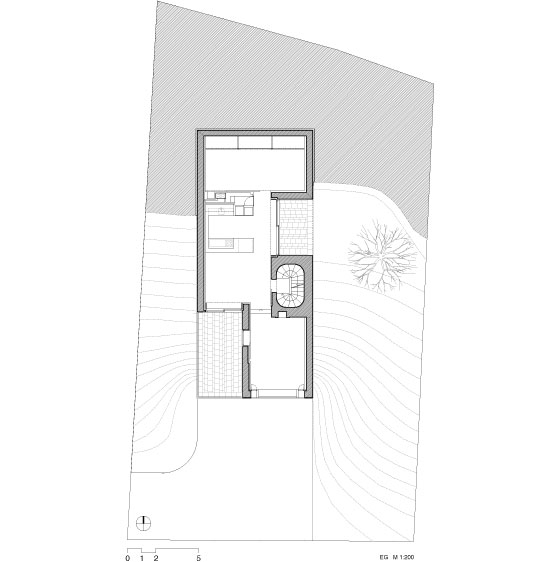
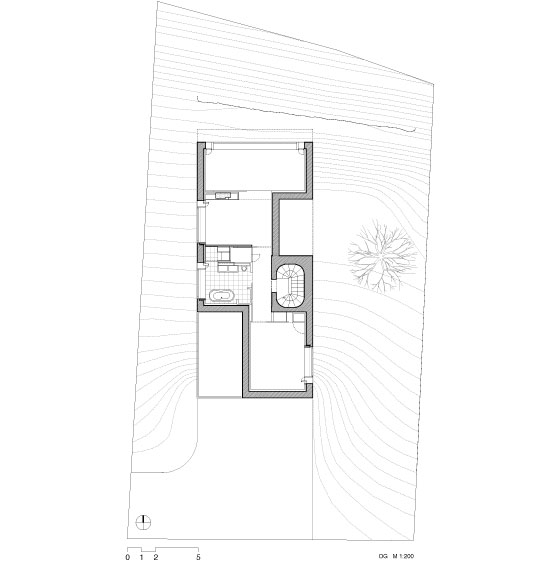
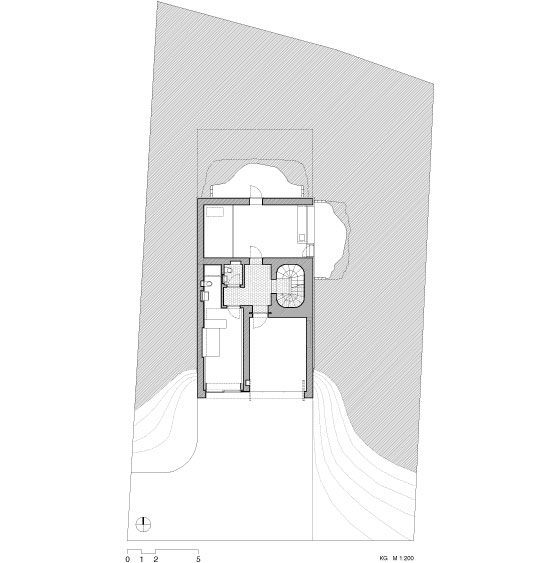
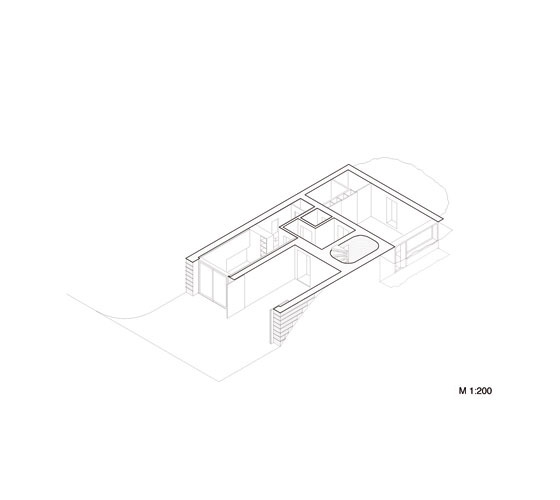
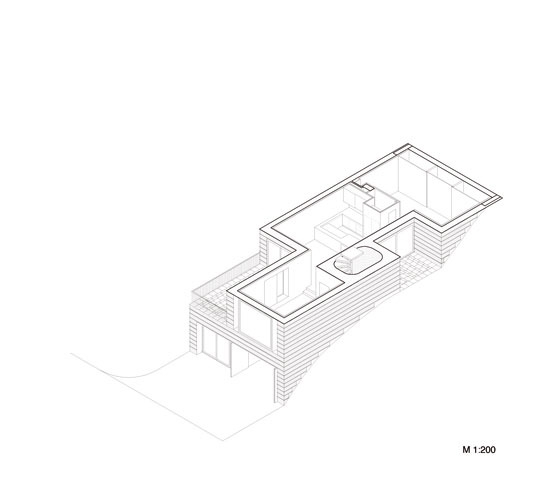
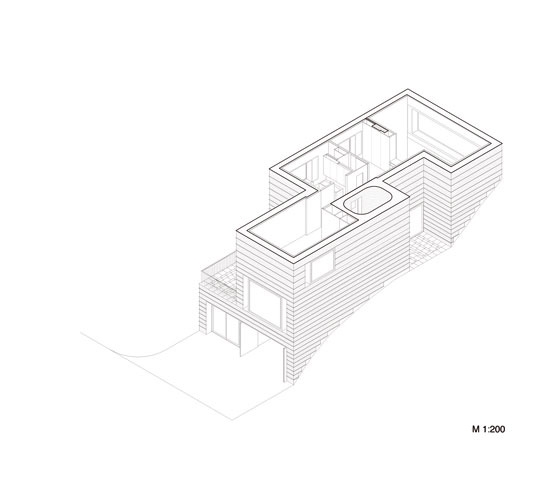
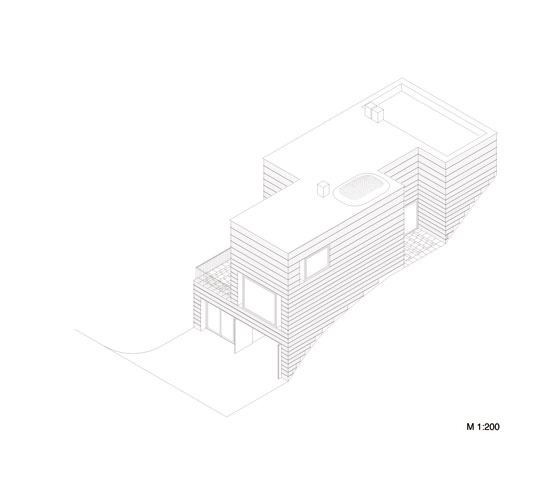
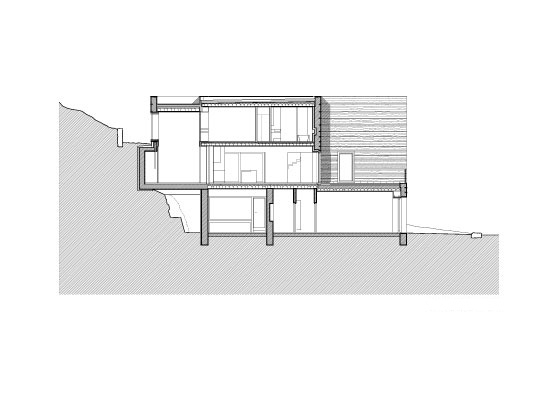
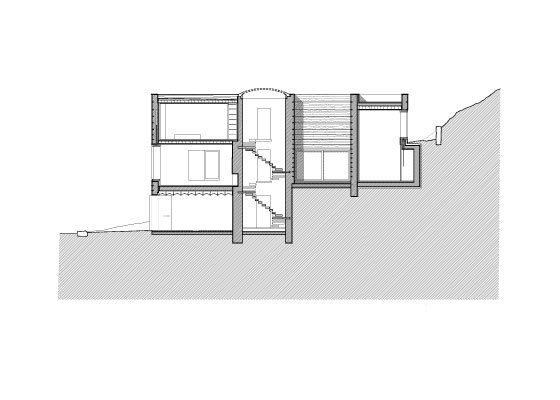
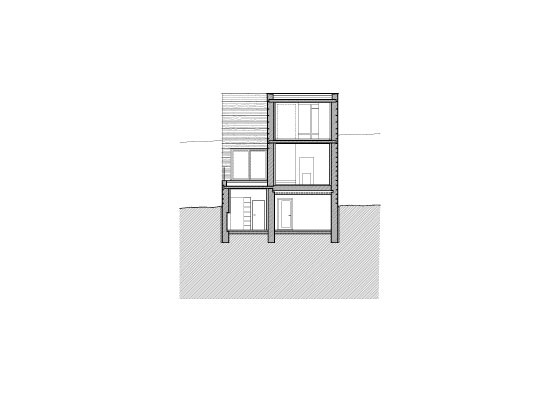
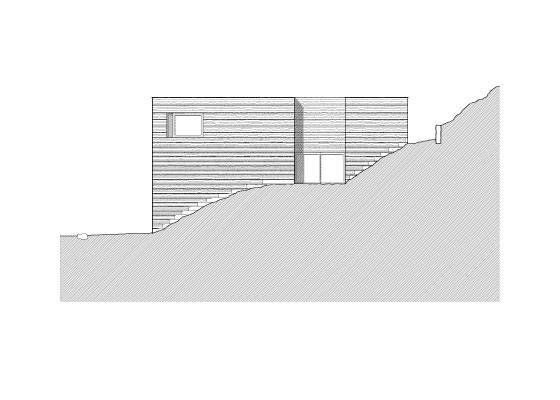
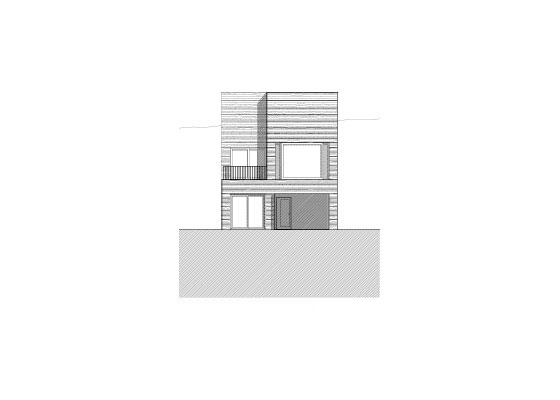
References
1- https://www.architectsnotarchitecture.com/archive/martin-rauch/
2- https://www.erden.at/
3- Rammed earth house, Rauch family home by Boltshauser Architekten | Detached houses (architonic.com)